Unlocking Potential: The Role of a Prototype Mold Factory in Modern Manufacturing
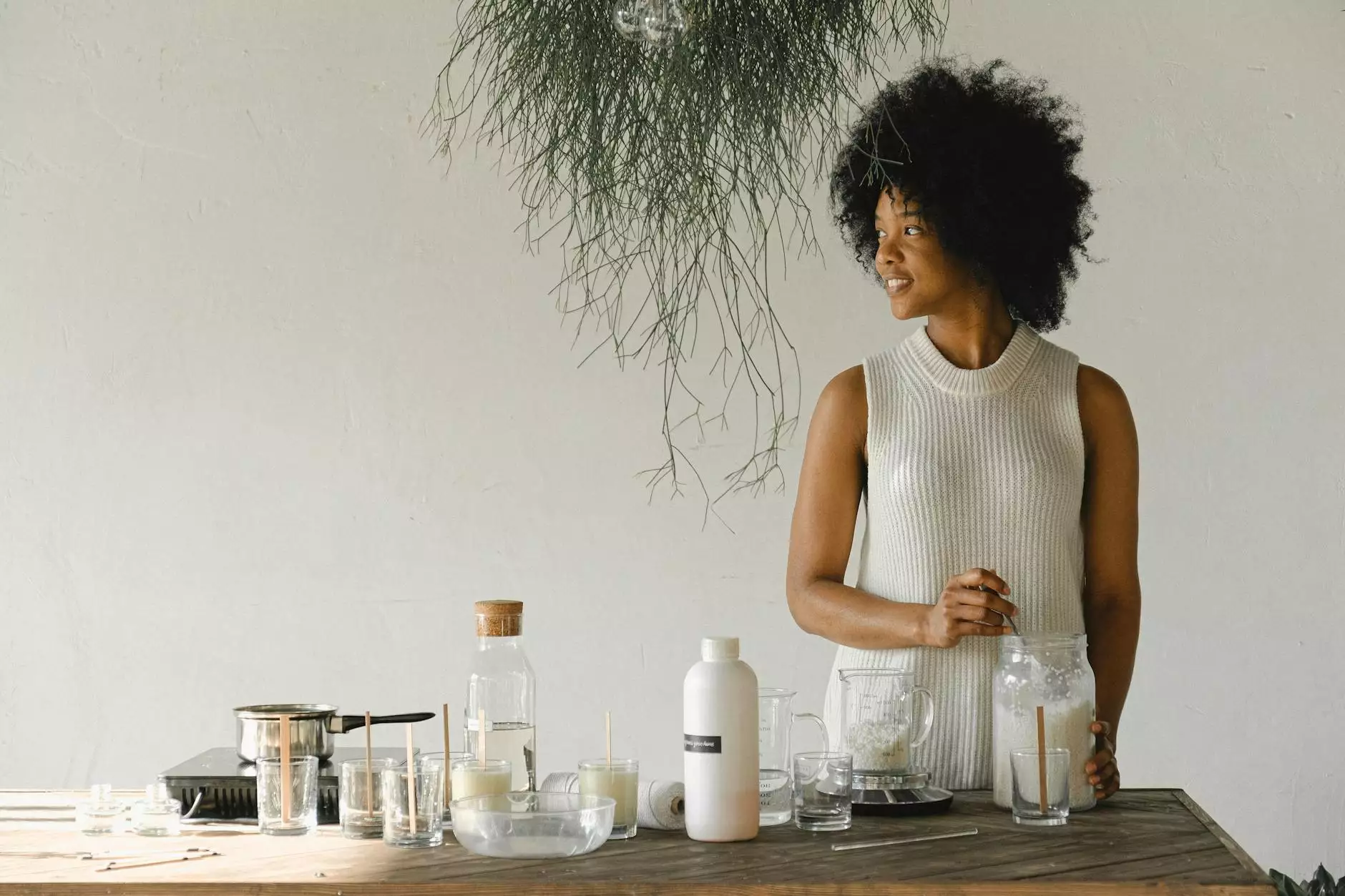
The world of manufacturing is continuously evolving, and at the forefront of this evolution is the prototype mold factory. These facilities play a pivotal role in the development of products across diverse industries. In this comprehensive guide, we delve into what a prototype mold factory is, the processes they employ, and the significance of their contributions to the manufacturing landscape.
Understanding Prototype Mold Factories
A prototype mold factory specializes in creating molds that are used to produce prototypes of products before they enter full-scale production. This critical phase allows designers and engineers to assess their designs practically and make necessary adjustments before committing to large quantities. By utilizing a prototype mold factory, companies can ensure that their products meet quality and performance expectations right from the start.
The Importance of Prototyping in Manufacturing
Prototyping serves several essential purposes in the manufacturing process:
- Validation of Design: Prototypes allow teams to validate the functionality and design of a product.
- Cost Efficiency: Catching design flaws early can save companies a considerable amount of money.
- User Feedback: Prototypes can be tested with real users, providing invaluable feedback that influences final design adjustments.
Key Processes Within a Prototype Mold Factory
Several technical processes are involved in the creation of molds in a prototype mold factory. Understanding these processes provides insight into the operational excellence of such factories:
1. Design and Engineering
Every successful prototype begins with meticulous design. Engineers and designers work together to create detailed specifications for the mold. Key tools used in this phase include:
- CAD (Computer-Aided Design) Software: Facilitates precise design and visual representation of the mold.
- FEA (Finite Element Analysis): Method to evaluate how the design will behave under real-world conditions.
2. Material Selection
The choice of materials is paramount in mold-making. Depending on the intended production volume and final product requirements, various materials can be used:
- Steel: Offers durability and is often used for molds that will see high production rates.
- Aluminum: A lighter option, ideal for prototypes that do not require extensive runs.
3. Precision Machining
Once the designs are finalized, the next step is precision machining. This involves creating the mold itself. Techniques used include:
- Milling: To shape the mold using rotating cutting tools.
- EDM (Electrical Discharge Machining): Ideal for intricate designs and shapes that are difficult to machine conventionally.
4. Assembly and Testing
After machining, the mold parts are assembled. This process is crucial and often involves testing the molds to ensure they meet specifications:
- Fit Testing: Checking that all components fit together seamlessly.
- Functionality Tests: Running trial products through the molds to ensure proper function.
Benefits of Utilizing a Prototype Mold Factory
Investing in a prototype mold factory brings several advantages to businesses aiming to elevate their products and operational efficiency:
1. Enhanced Product Quality
With prototypes, companies can pinpoint issues before mass production, leading to higher-quality end products. This proactive approach minimizes errors and ensures customer satisfaction.
2. Shorter Time to Market
By effectively utilizing prototype molds, businesses can significantly reduce the time it takes to get a product from concept to market. Agile prototyping techniques enable rapid iterations, allowing teams to respond to market demands swiftly.
3. Competitive Advantage
Companies that embrace prototyping often outrun their competitors by consistently innovating and improving their product offerings.
Choosing the Right Prototype Mold Factory
Not all prototype mold factories are created equal. When selecting a manufacturing partner, consider the following criteria:
1. Expertise and Experience
Look for a factory with a proven track record in producing molds similar to your requirements. Experience often correlates with quality and reliability.
2. Technology and Equipment
Investigate the technology used in the factory. Advanced equipment usually results in higher precision and better outcomes.
3. Consultation and Support
A good prototype mold factory should offer support throughout the process, from initial design to final testing.
Conclusion: The Future of Prototype Mold Factories
As industries continue to evolve and innovate, the role of the prototype mold factory becomes increasingly valuable. By harnessing the power of prototyping, businesses can streamline their processes, enhance product quality, and maintain a competitive edge in a rapidly changing market.
In summary, choosing to partner with a reputable prototype mold factory can transform how you approach product development, ensuring you deliver world-class products that meet the needs of your customers and thrive in the competitive landscape.
Ready to Get Started?
If you’re looking to innovate with your product designs and need a reliable prototype mold factory, consider contacting us at deepmould.net. Our experienced team is ready to assist you in bringing your ideas to life through expert mold-making services.